Applications and usage examples
- Search by surface function
- Search by processing effect
Reduce weight
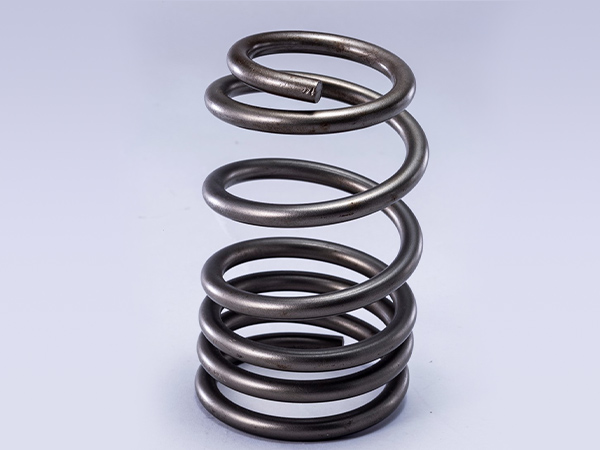
Strengthen
Automobiles
Use shot peening to reduce the weight of suspension springs
Reduce energy loss
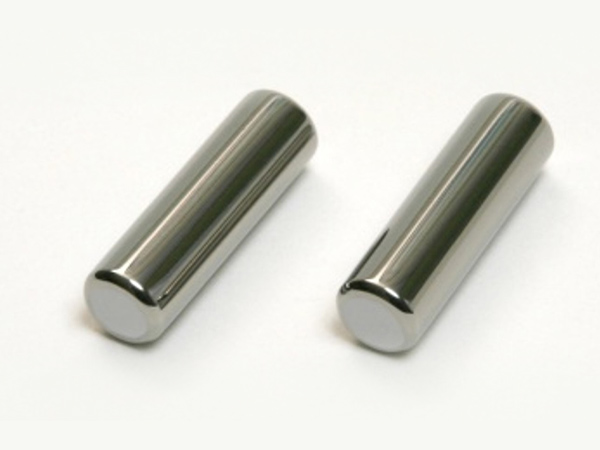
Polish
Bearings
Use oil-reservoir processing to improve the sliding performance of bearing rollers
Increase yield
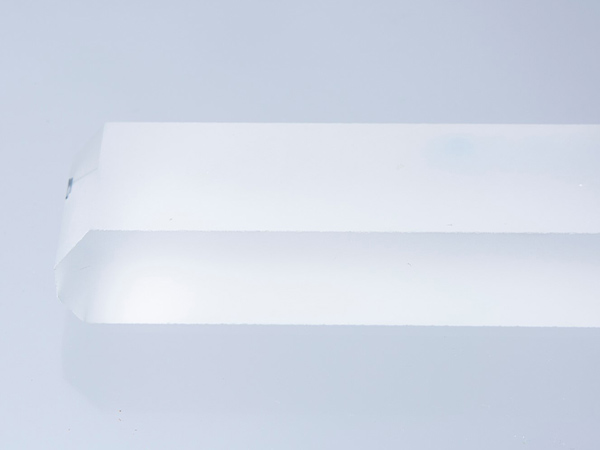
Peel
Electronics
Remove the damaged layers of wafers to increase yield
Deburr
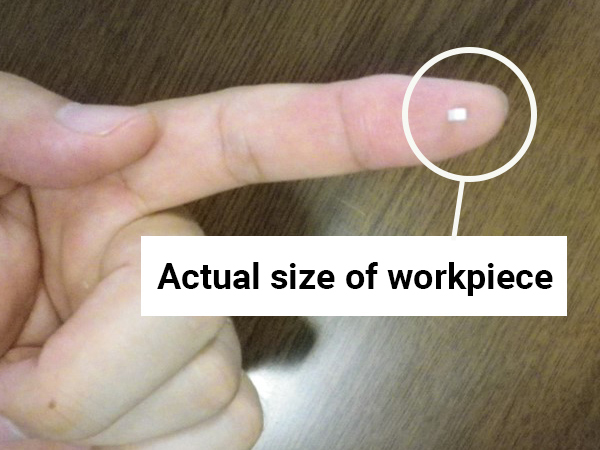
Remove
Electronics
Use a powder suction process to deburr micro-products
Create peel-resistant coating
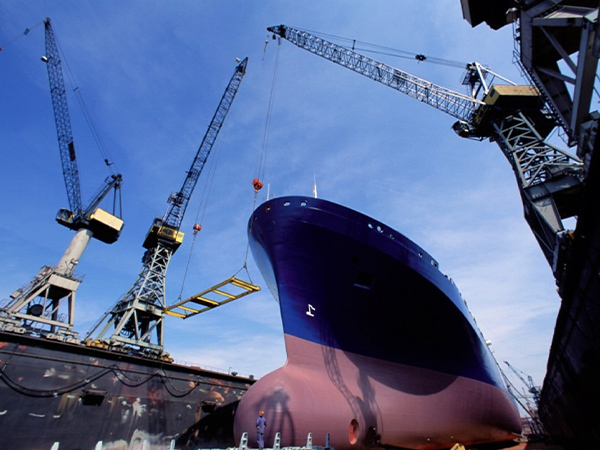
Roughen
Shipbuilding
Use shot blasting on steel plates for ships for surface roughening
Process printed circuit boards
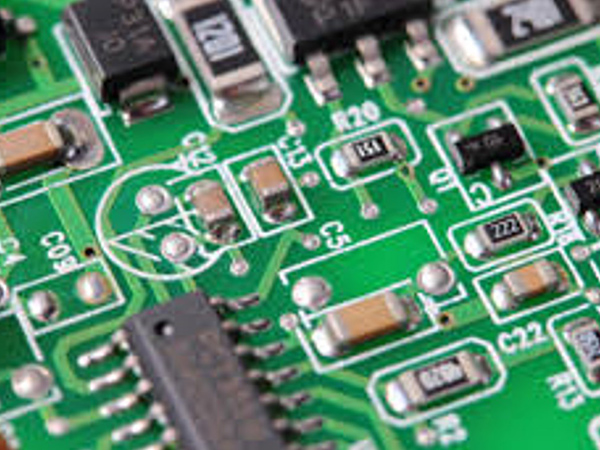
Microprocessing
Electronics
Use microblasting on printed circuit boards for damage-free fine-hole processing
Visually track effects
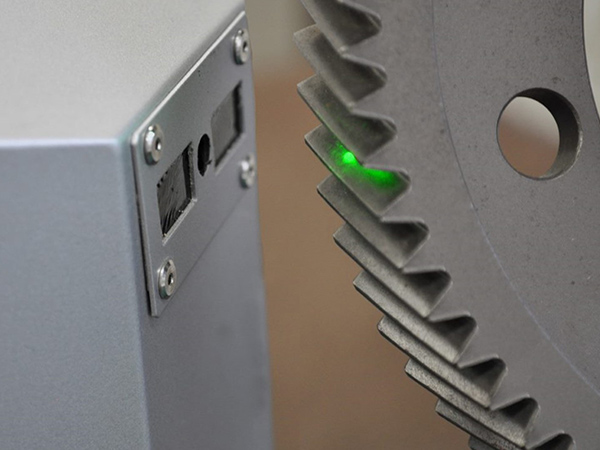
See
Test/measure
Use X-ray stress measurement to visually track all peening stress values
Prevent joint loosening
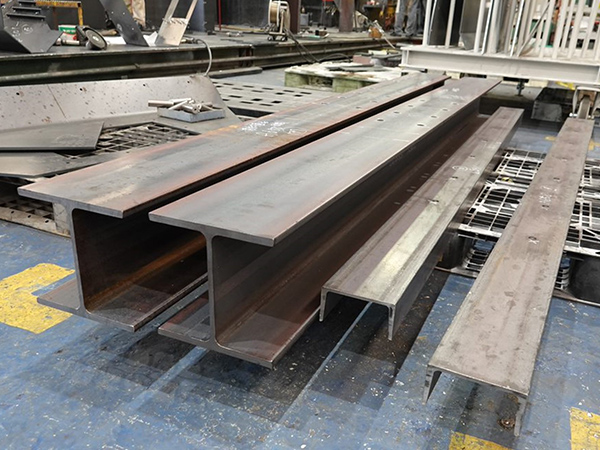
Roughen
Steel frames
Use shot blasting on steel frame members to roughen their surfaces for the optimal sliding coefficient
Stabilize deposition quality
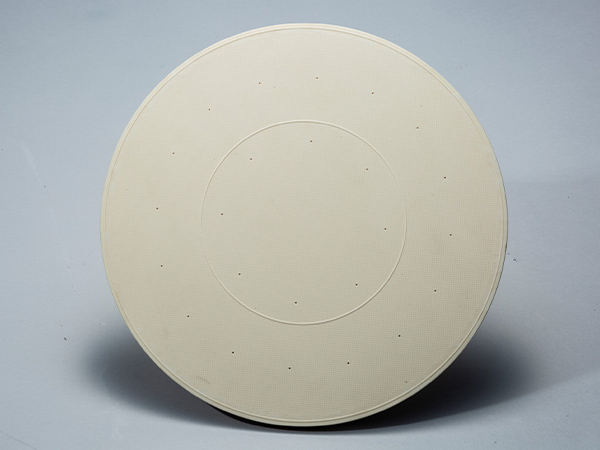
Microprocessing
Electronics
Use precision embossing on electrostatic chucks to ensure uniform pin height
Remove scaling
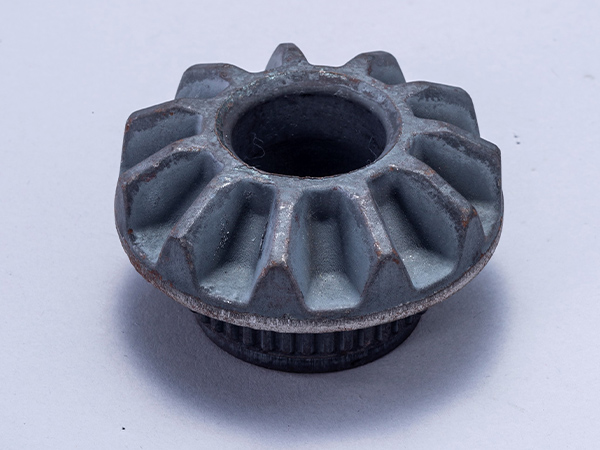
Peel
Forging/heat treatment
Use shot blasting on heat-treated products to remove scaling
Deburr
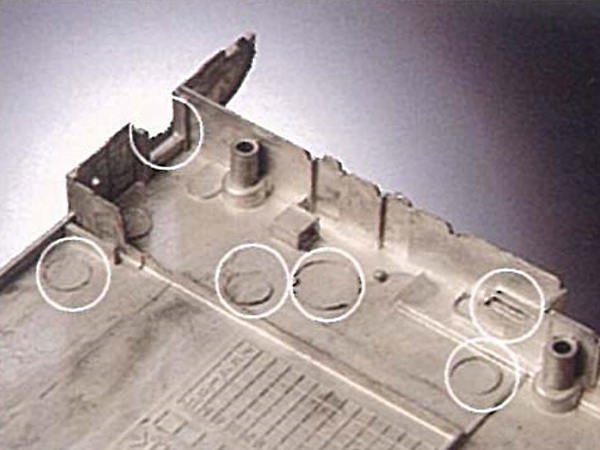
Remove
Diecasting
Use shot blasting on thin-walled products for strain-controlled deburring
Reduce friction coefficient
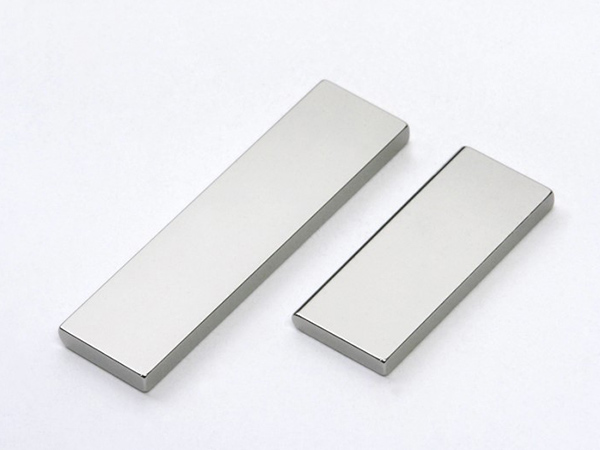
Polish
Compressors
Smooth-polish compressor vanes to improve sliding performance
Add traceability
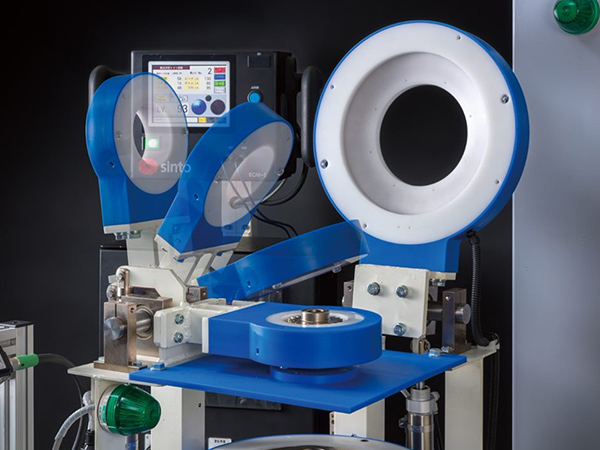
See
Test/measure
Use non-destructive testing for total in-line testing of peening process aptitude
Lengthen product life
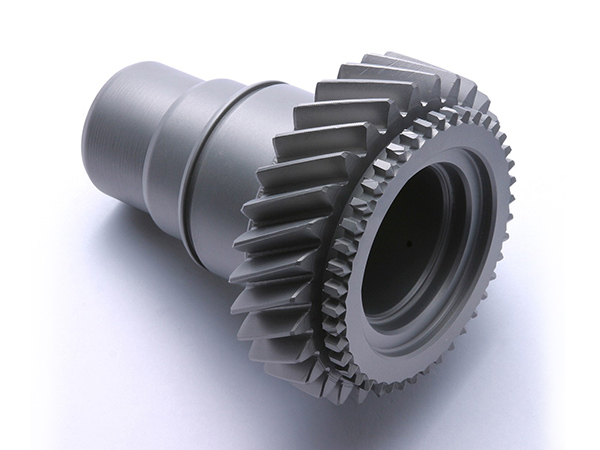
Strengthen
Automobiles
Use shot peening on gears to prevent cracking
Remove scaling
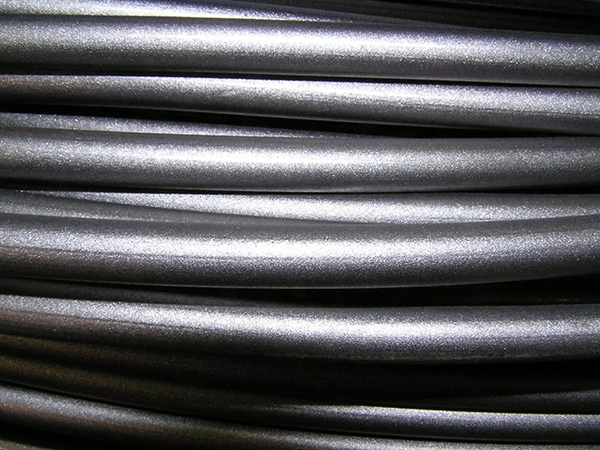
Peel
Wire
Use shot blasting on wire to remove scaling
Improve coating adhesion
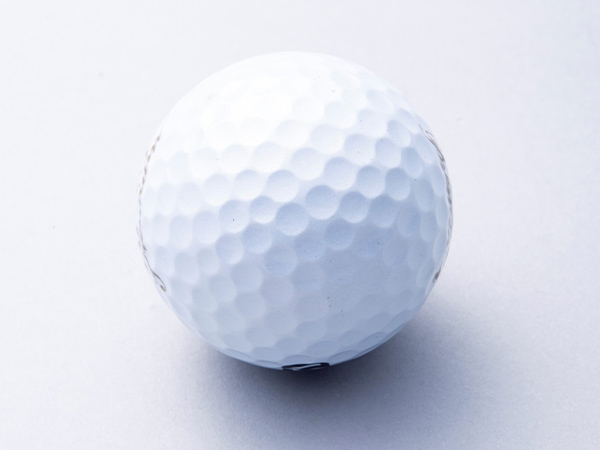
Roughen
Commodities
Use air blasting on golf balls for roughening
Precision wafer processing
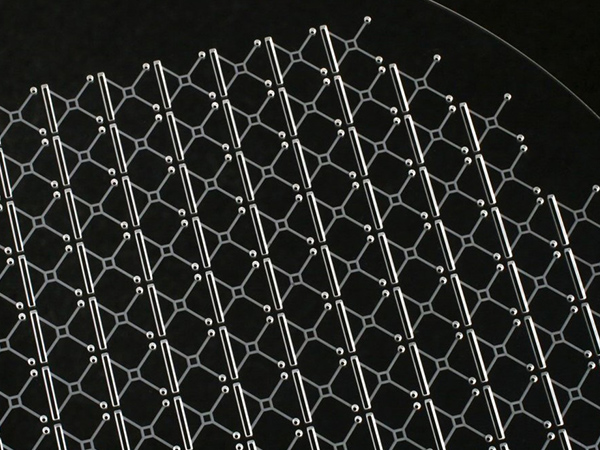
Microprocessing
Electronics
Use microblasting on electronic substrates for hole and groove processing
Deburr
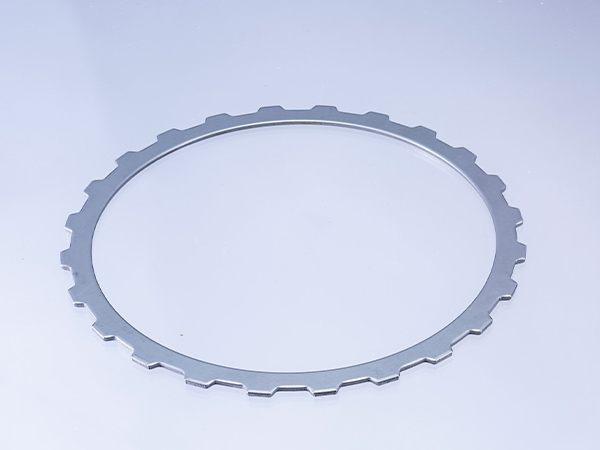
Remove
Automobiles
Use planetary brush polishing on thin press products to deburr the ends
Check effectiveness criteria
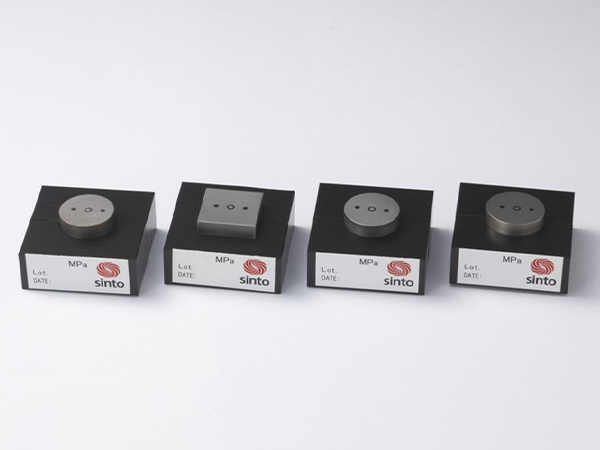
See
Test/measure
Use stress reference pieces to improve the reliability of X-ray stress measurements
Ensure reliable quality
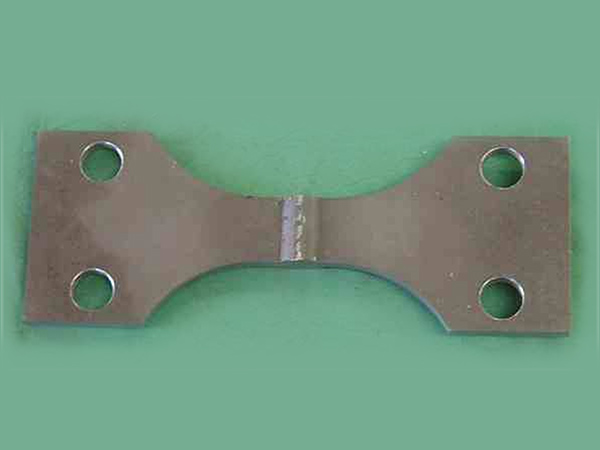
Strengthen
Automobiles
Use shot peening to increase the rigidity of plate welding
Smooth complex shapes
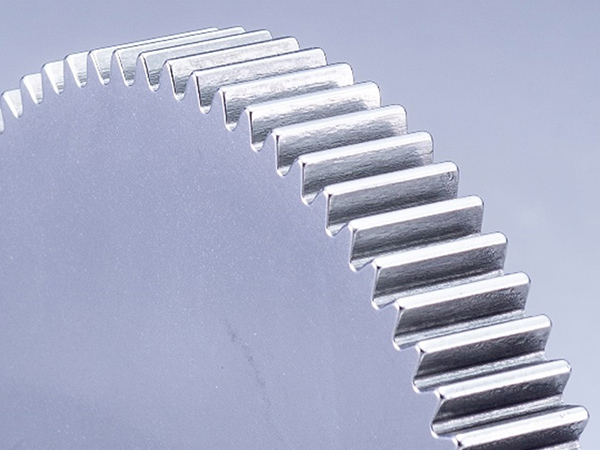
Polish
Gears
Use a smoothing process on gears to smooth out complex shapes
Remove foundry sand
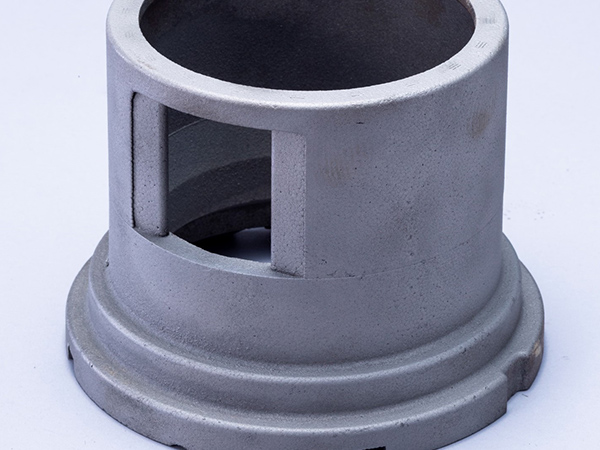
Peel
Casting
Blast casting parts to remove foundry sand
Increase durability
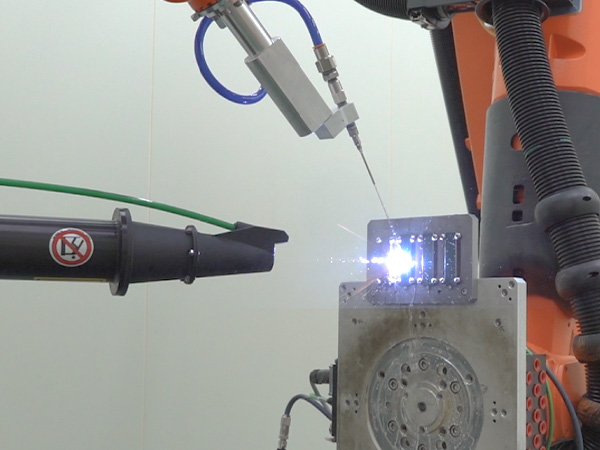
Strengthen
Aircraft
Use laser peening on turbine blades to increase corrosion resistance
Deburr
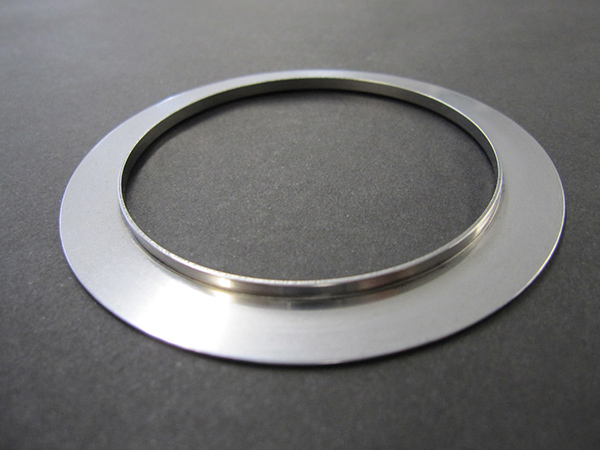
Remove
Bearings
Use barrel polishing on thin-walled/small parts to remove burrs
Reduce foundry defects
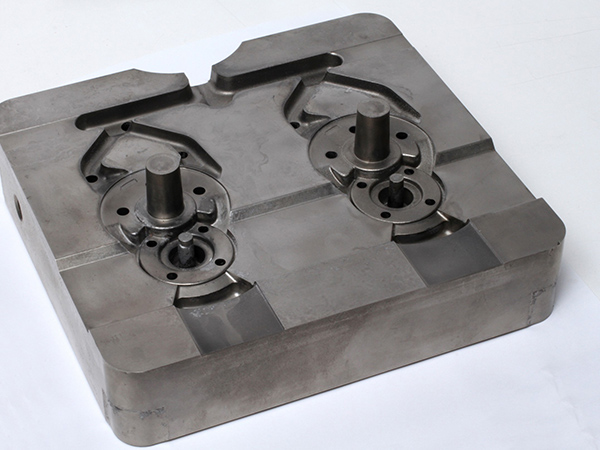
Roughen
Diecasting
Form dimples on diecast dies to reduce defects
Form carbon fiber
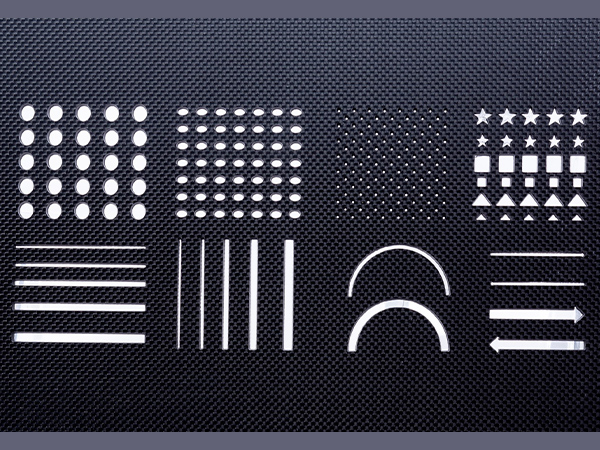
Microprocessing
Aircraft
Use microblasting on CFRPs for patterning processing
Create smooth motion
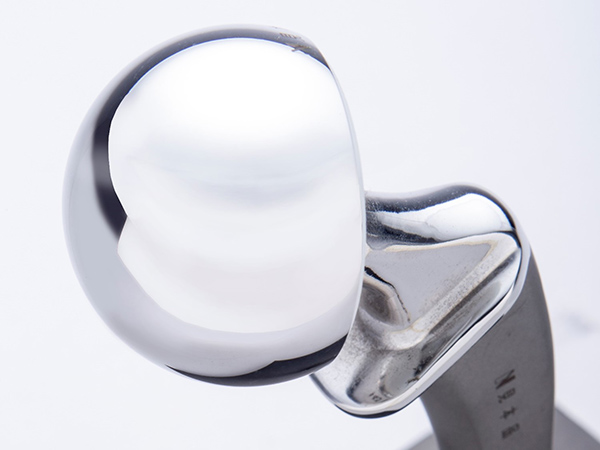
Polish
Healthcare
Smooth-polish artificial joints to improve sliding performance
Measure surfaces
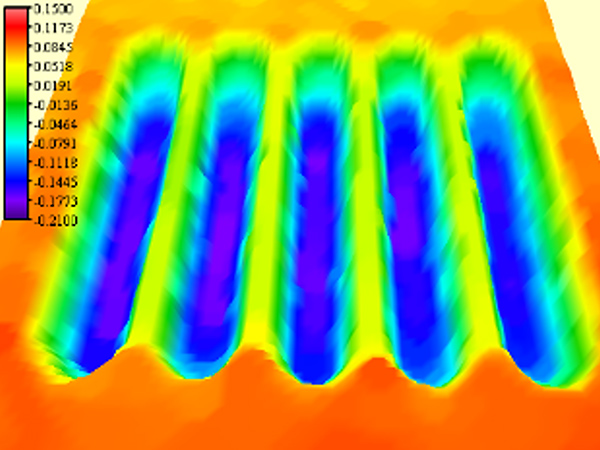
See
Test/measure
Use contactless measurement to assess surface roughness and 3D shape
Please consult us for inquiries.
+81-52-581-6896
Available hours: 9:00-12:00 and 13:00-17:00 JST, Monday through Friday
(excluding national and corporate holidays)